Talaris : a hydraulically operated ankle exoskeleton
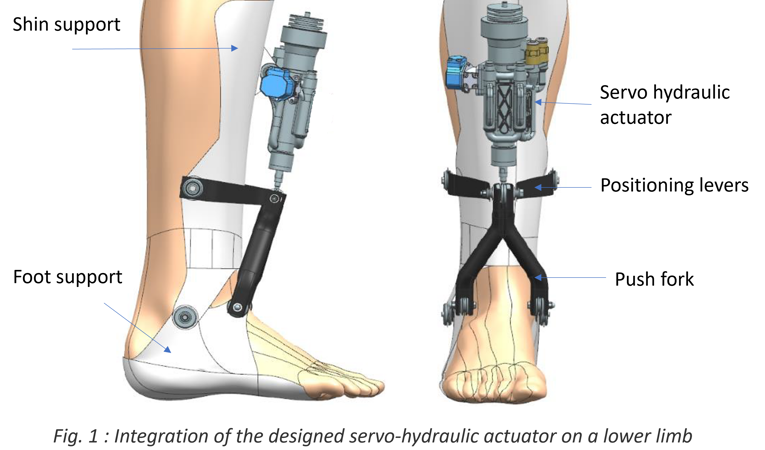
Preliminary design and testing of a hydraulic actuator for an autonomous ankle exoskeleton
The aim of the project was to study the engineering feasibility of a motorized ankle-foot orthosis for use in rehabilitation therapy (s. Fig. 1 above). More specifically, the project focused on the development of a hydraulic actuation system for an ankle exoskeleton capable of delivering a peak power of 250 W, with a maximum torque of 90 N.m and a maximum angular speed of 320 degrees per second. The question we wanted to answer was “How far could we reduce the weight of such a hydraulically-operated orthosis without sacrificing dynamics or power?”
Two candidate hydraulic actuation concepts were envisaged, namely a servo-hydraulic actuator (SHA) and an electro-hydrostatic actuator (EHA). We performed a preliminary design for both concepts, selected adequate components available from the market, and conducted simulations with the software Simcenter Amesim to compare their performance.
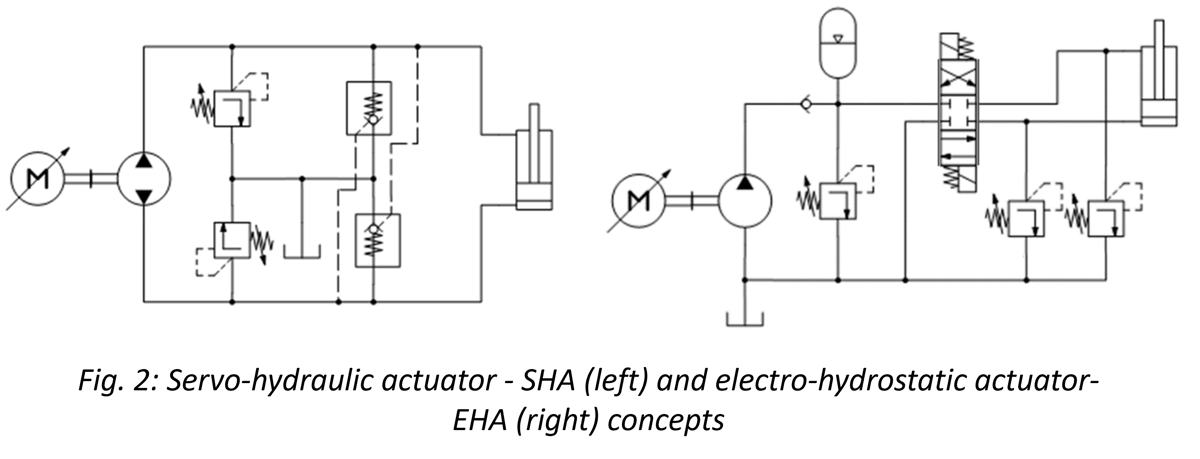
Choosing between EHA and SHA is choosing between two conflicting objectives – namely dynamics versus light distal weight – that is inevitably frustrating in applications like exoskeletons where both are equally important.
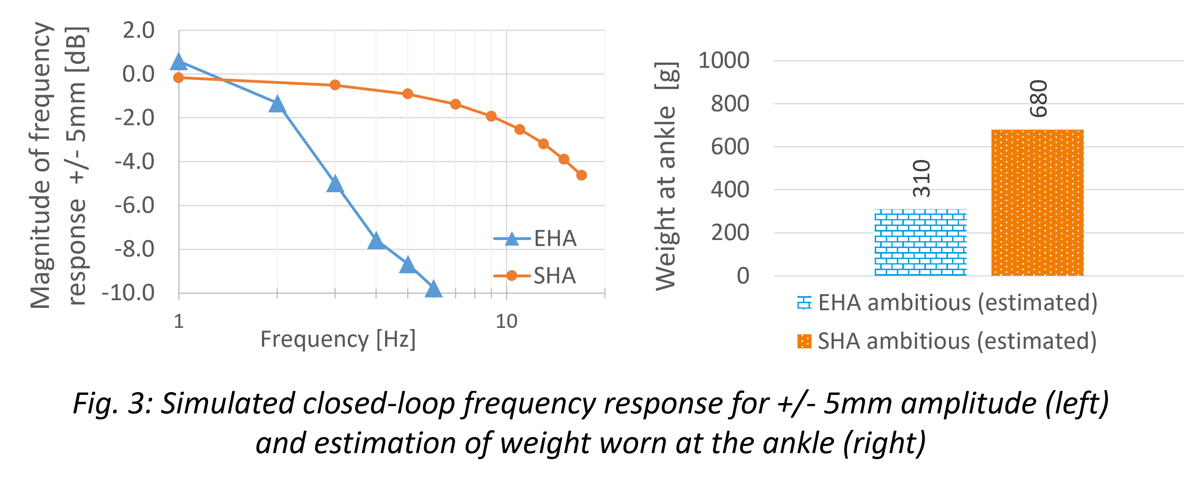
Our simulation results revealed that the lower dynamic performance of the EHA would be too critical for our application and the SHA concept was retained for the following phase of the project. A first functional prototype was built and tests demonstrated adequate dynamic performance at normal walking speed, see figure 4.
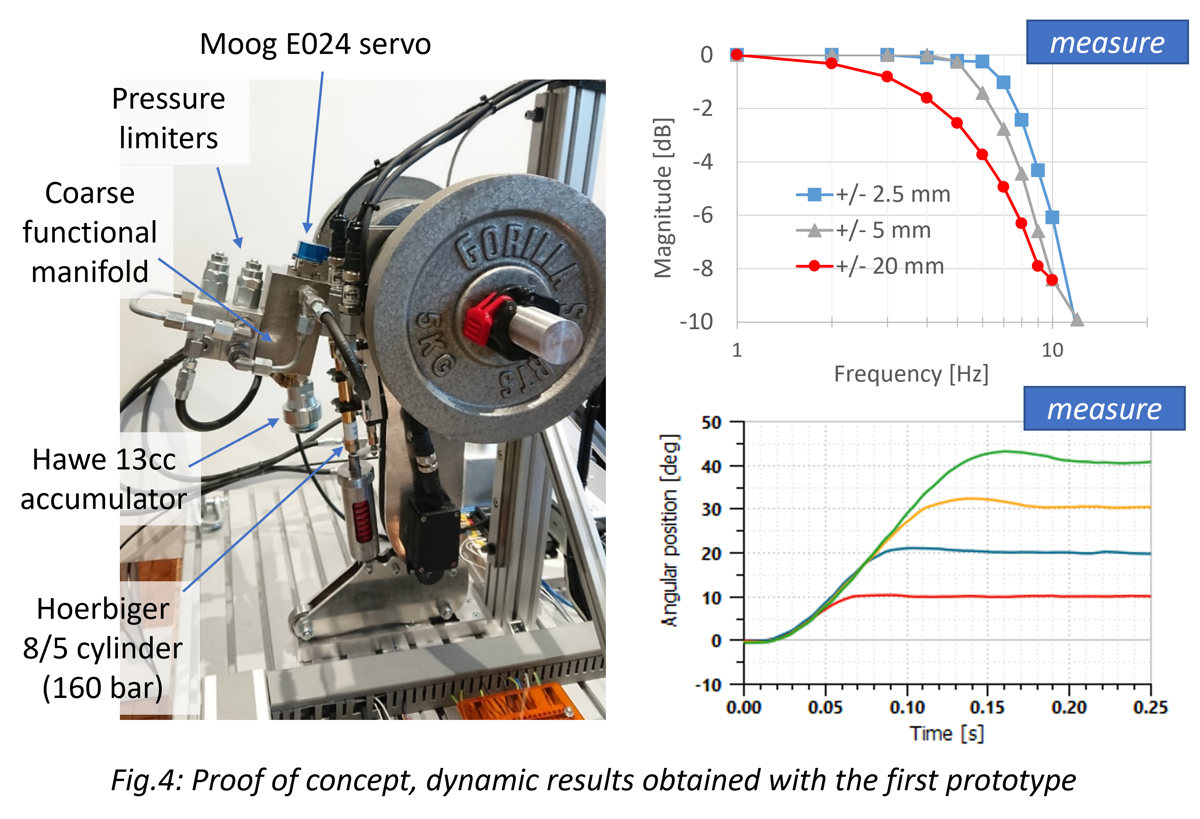
A detailed design was then proposed, combining commercially available components with a custom-made aluminum manifold incorporating the hydraulic cylinder. The actuator design results in a total pin weight of just below 1.0 kg. An alternative design was also proposed to lower the weight down to 0.67 kg thanks to a hydraulic manifold made by selective laser melting, see figure 5.
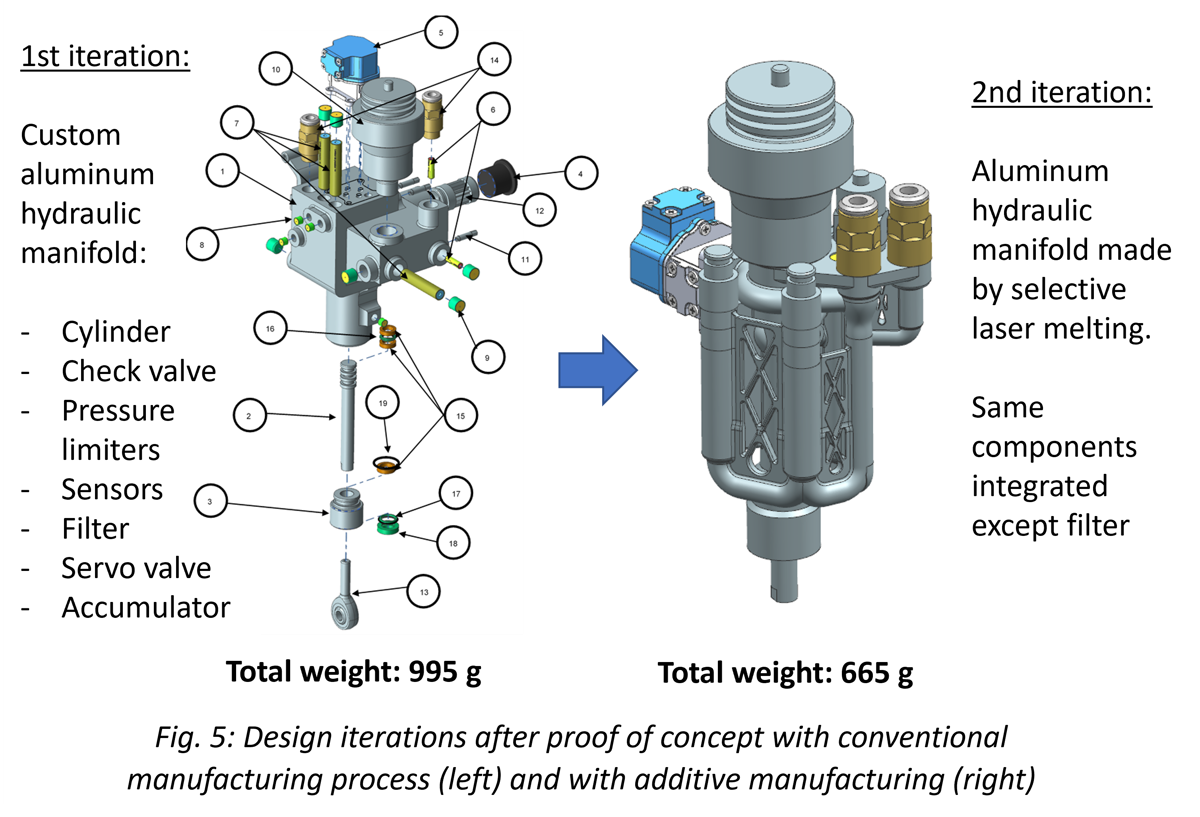
Finally, a carbon fiber brace was designed and manufactured to interface the actuator on a lower limb, see figure 6. The total mass of the brace, inlcluding the carbon fiber parts and all necessary metal inserts is 0.75 kg, which would bring the total mass (actuator + brace) to around 1.4 kg with the 3D printed version of the actuator.
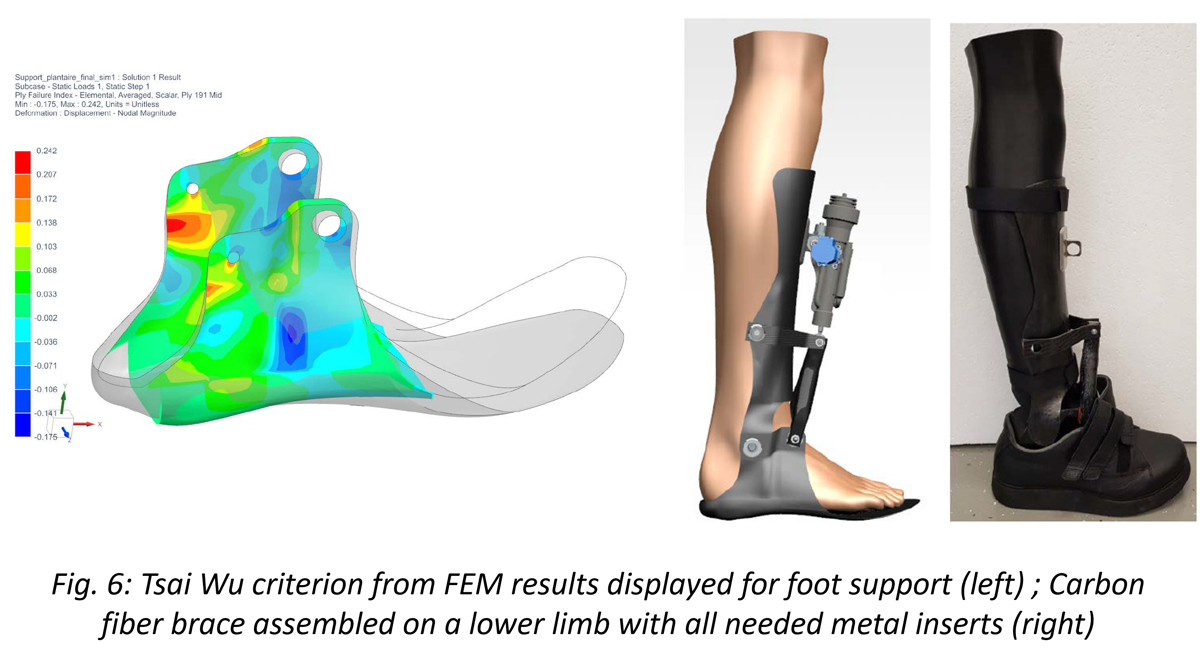
Despite the interest that the project aroused in the working groups to which it was presented, it was not possible to find a viable ecosystem, combining the fields of health and technology, to pursue the development and the project ended in 2021.
Publications related to the project:
E. Viennet and L. Bouchardy, Paper in the proceedings of the 12th International Fluid Power Conference, 12-14 October 2020, Dresden, Germany
Reducing time and cost of testing by using a virtual platform, Case Study on the siemens website, retrieved 10 December 2024
S. Baeriswyl, Entwicklung eines Hydraulikblockes mit integriertem Hydraulikzylinder, Bachelor thesis 2019, HEIA-FR
G. Leva, Etude d’un bloc hydraulique en impression 3D, Bachelor thesis 2020, HEIA-FR
R. Yerly, Développement d’une structure en composite pour un exosquelette de cheville, Bachelor thesis 2020, HEIA-FR
D. Vallélian, Conception et fabrication d’une structure en composite pour une orthèse de cheville, Bachelor thesis 2021, HEIA-FR