- Research Projects : /en/applied-research/institutes/irap/research-projects/
- Infrastructure : /en/applied-research/institutes/irap/infrastructure/
- Team : /en/applied-research/institutes/irap/team/
- Agenda : /en/applied-research/institutes/irap/agenda/
- News : /en/applied-research/institutes/irap/news/
- Education : /en/applied-research/institutes/irap/education/
- Contact and acces : /en/applied-research/institutes/irap/contact-and-acces/
- Research Projects : /en/applied-research/institutes/irap/research-projects/
- Infrastructure : /en/applied-research/institutes/irap/infrastructure/
- Team : /en/applied-research/institutes/irap/team/
- Agenda : /en/applied-research/institutes/irap/agenda/
- News : /en/applied-research/institutes/irap/news/
- Education : /en/applied-research/institutes/irap/education/
- Contact and acces : /en/applied-research/institutes/irap/contact-and-acces/
Upgrading of 100% biobased composites
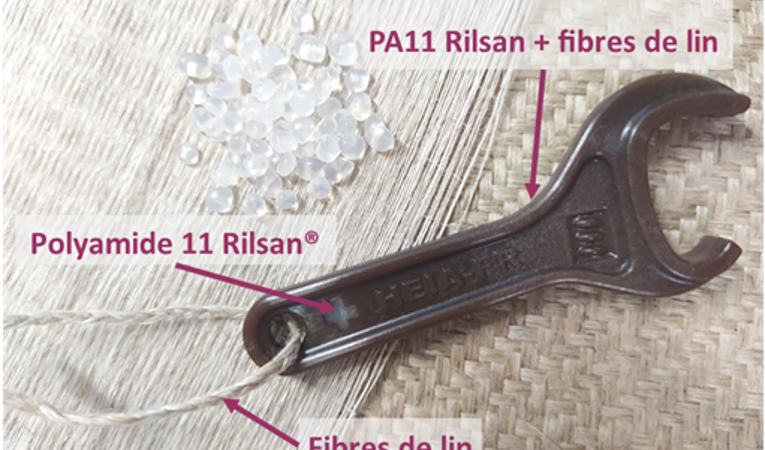
Summary
Composites and design of lightweight structures
Travail de Bachelor
BComp
Benoît Grelier
Skills directory
February 2021 - June 2021
Concrete revalorisation of a 100% biosourced composite material through the use of simple and controlled processes

Article from the magazine Kunstoff Xtra and translated from French to English. Link to the article
Manufacturing biosourced composite materials and successfully recycling them for industrial applications are fully in line with the problems linked to the circular economy. This Bachelor's work, carried out at the iRAP / HES-SO Fribourg institute and in partnership with the companies Bcomp Ltd. and Arkema, illustrates the concrete revalorisation of a 100% biosourced composite material through the use of simple and controlled processes.
Continuous fibre composite materials are mainly composed of synthetic materials, which are polluting and non-recyclable. This is why they represent a challenge to combine mechanical properties, respect for the environment and sustainability. With the growth of bio-based products on the market, it is now possible to consider the manufacture of composite parts whose reinforcements and matrix are entirely bio-based and recyclable.
For certain fields, such as wind energy, these solutions would alleviate the issues related to resources and recycling. Indeed, wind turbine blades are currently made from synthetic fibres and thermosetting resins, and are usually buried or incinerated at the end of their life. The work is therefore part of the revaluation of biosourced composite plates that could be used to make the shells of wind turbine blades.
This project relied on the skills and resources in thermocompression, plastic injection, compounding, observation and characterisation of materials of the laboratory of light structures and the institute of Applied Research in Plastics (iRAP), attached to the University of Engineering and Architecture of Fribourg (HEIA-FR).
Recycling a biobased composite
The selection of biobased materials was based on flax fibres supplied by Bcomp and the thermoplastic resin Polyamide 11 Rilsan, derived from castor oil, from Arkema. The thermoplastic nature of the resin means that it can be reshaped after heating, allowing it to be reused. Based on this choice, composite sheets with 64% fibre content were manufactured by thermocompression using a heated press.
These composite plates were then crushed to obtain a biosourced material (Fig. 1). Analyses of this material were carried out and showed that it can be reshaped at up to 210°C (the degradation temperature of flax fibres). As the melting point of Polyamide 11 Rilsan is around 190°C, low-temperature processes can be used, thus requiring little energy. Viscosity analyses (Melting Flow Index - MFI) have also shown that the crushed composite is sufficiently fluid to be injected at a maximum fibre content of around 40%.
Reshaping processes
To reshape the crushed composite, the targeted manufacturing process is plastic injection. For this purpose, it is necessary to transform this material into an injectable granulate with a homogeneous fibre content by adding pure Polyamide 11 Rilsan. Two compoundings of the recycled material were made at 20% and 40% recycled fibre (i.e. 33% and 62% recycled composite respectively).
Tensile specimens were then injected with the two batches of material from the compoundings. The injection cycle of these parts was parameterised in order to define the optimal temperatures and pressures for reshaping the recycled composite and to avoid its degradation during the processes. An additional study was carried out on a possible third life for the biosourced composite. The parts injected with 20% fibre were crushed and injected again.
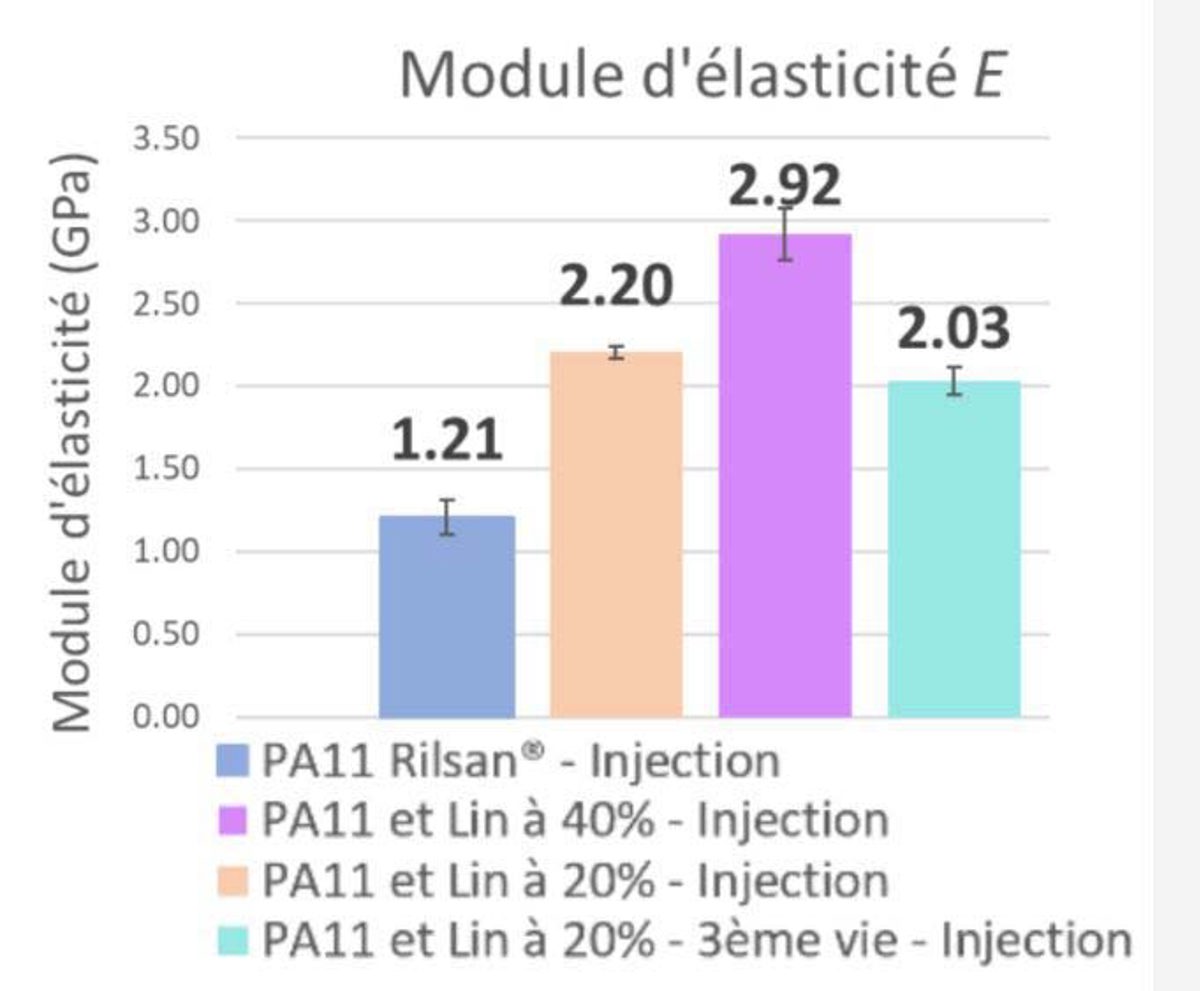
Injected test pieces were used to characterise the recycled composite after grinding, compounding and injection. Density, stiffness, strength and elongation at break were measured (Fig. 2).
Recycled composite upgrading
The results highlight the stiffening effect of the material thanks to the flax fibres. Indeed, even when recycled, flax fibres give additional stiffness to Polyamide 11. There is therefore an interest in using this biosourced and recycled composite. The tests also make it possible to envisage several life cycles for this material while maintaining its interesting properties.
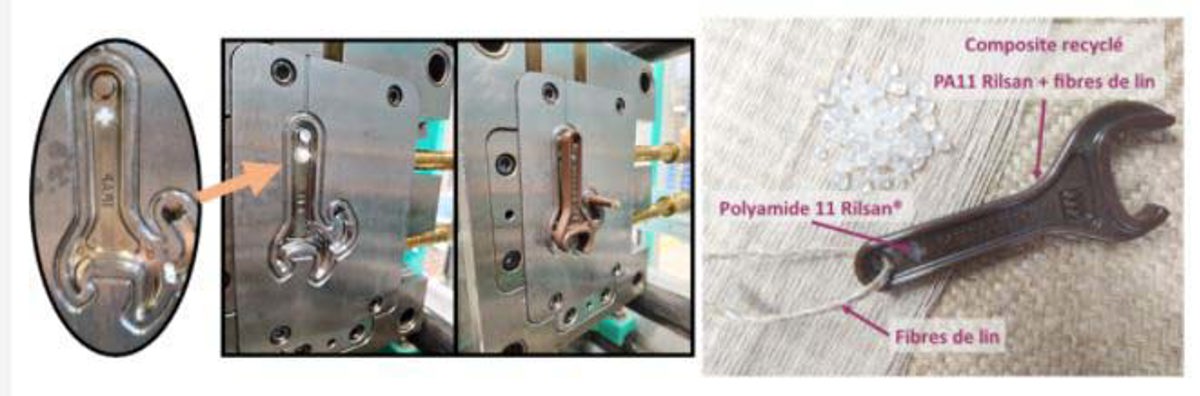
This project considered the recycling and upgrading of a 100% biobased composite for industrial applications such as assembly or reinforcement parts in a wind turbine blade. To illustrate this, two series of key-ring objects were injected according to the optimised parameters and also adding an overmoulding operation (Fig. 3).
In the context of the circular economy, the industry can find, through this project, a solution for the revalorisation of biosourced composite parts at the end of their life or for the recycling of production waste.
By Léonie Marchand, Mechanical Engineering graduate HEIA-FR 2021; Benoît Grelier and Laure Dupuits: HES professors in plastics and light structures