- Research Projects : /en/applied-research/institutes/irap/research-projects/
- Infrastructure : /en/applied-research/institutes/irap/infrastructure/
- Team : /en/applied-research/institutes/irap/team/
- Agenda : /en/applied-research/institutes/irap/agenda/
- News : /en/applied-research/institutes/irap/news/
- Education : /en/applied-research/institutes/irap/education/
- Contact and acces : /en/applied-research/institutes/irap/contact-and-acces/
- Research Projects : /en/applied-research/institutes/irap/research-projects/
- Infrastructure : /en/applied-research/institutes/irap/infrastructure/
- Team : /en/applied-research/institutes/irap/team/
- Agenda : /en/applied-research/institutes/irap/agenda/
- News : /en/applied-research/institutes/irap/news/
- Education : /en/applied-research/institutes/irap/education/
- Contact and acces : /en/applied-research/institutes/irap/contact-and-acces/
PubicMask
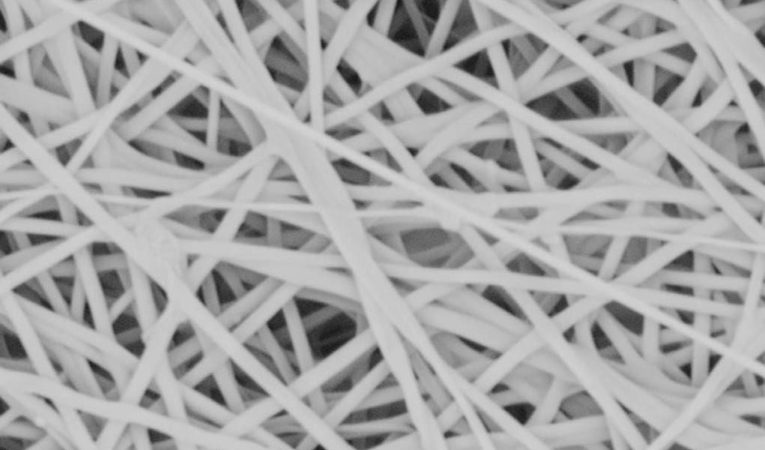
Summary
Surface technologies and nanotechnologies
HES-SO Impulse Research Fund
HE-Arc
Stefan Hengsberger
Skills directory
January 2021 - February 2023
Development of a disposable protective mask filter for the general public using electrospinning of a biodegradable polymer
Facemasks have gained unexpected attention during the Covid-19 pandemic. The high and sudden demand of facemasks has caused a serious shortage during several weeks on the Swiss market. Additionally, entire cargo of facemasks coming from Asian countries had to be destroyed since they did not meet the minimum requirements. This experience underlines the importance that Europe must become more independent from Asian products in such exceptional conditions. To avoid a new increase of the infection curve the public must accept to wear a facemask when the minimum social distancing cannot be respected. The use of facemasks on public places, during events like live concerts or demonstrations as well as on beaches will necessarily lead to facemasks that are thrown away in nature. Biodegradable disposable facemasks are therefore a first step to avoid an increasing pollution of the environment.
The target group of our PublicMask project are people who areless exposed to viruses and who make a less responsible use of the facemask.
In the context of our PublicMask project stakeholders in the field of biomedical engineering, industrial chemistry, plasturgy and nanotechnology have collaborated. The goal was to develop a biodegradable filter for a use in disposable facemasks. This filter will has been fabricated by electro-spinning. This method allows for a fabrication of thin continuous polymer fibers by accelerating a polar polymer/solvent mixture with an electric field. A dense network with fibers of less than 1 micrometer in diameter can be obtained what is efficient to absorb particles of the typical size of viruses.
The innovative part of this project was the development of biodegradable filters using a polyester-amide grade that has been developed 'in-house' by the ChemTech institute at HEIA-FR. ChemTech tuned the polymer/solvent mixtures to achieve a viscosity that is adapted to the electro-spinning process. The medical devices group at HE-Arc set up and optimized the electro-spinning process in a first step with a solvent-based polymer solution. A filter test stage has been developed by iRAP at HEIA-FR. The filter must fulfill two main requirements, high virus absorption and a high air transmission. For the efficiency test the filter material has been exposed to a continuous air flow containing plastic microparticles. The goal was the production of a biodegradable filter that performs at least as well as the polypropylene based filter of standard disposable masks. A biodegradation test of the filter has been successfully performed. Furthermore, the fabrication of the filter applying melt-spinning has been successfully demonstrated, what is an economically and ecologically interesting process. Melt-spinning allows for producing fibers of molten polymer what avoids the use of (toxic) solvents.
Overall, the results of this project pave the way for the development of high-performance biodegradable facemasks based on biosourced PEA. Future studies will address the ideal combination of melt-spinning and electrospinning process to fabricate an entire facemask. The studies will also include water vapor transmission rate and wearing comfort. The potential final costs of a disposable biodegradable facemask will also be evaluated and factors like the upscaled PEA synthesis and a production including an electrospinning step will be considered.